Problems with Plastic Musical Instruments: Five Things to Consider
May 18th, 2020
5 min read
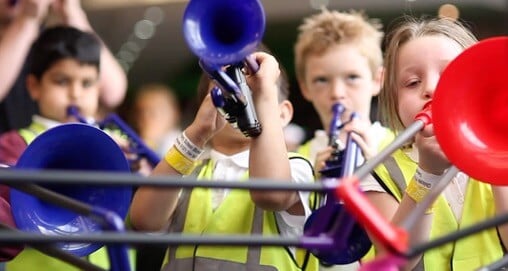
Here at Warwick Music Group, we care most of all about getting children started in music – because music matters – and it's our desire to help make the journey accessible and fun for everyone!
You might think it strange for a manufacturer of plastic musical instruments to be writing a blog on potential problems but as the world’s leading manufacturer of plastic trumpets and trombones, we think it's important to share these with you before you buy; if a plastic instrument isn’t the right choice for you, you shouldn’t buy one!

Having said that, we don’t want you to automatically discount plastic instruments either; the most important thing is finding the right product for you/your child - why? So you have a successful first experience in making music!
In the modern world, these words have never been more true: “You never get a second chance to make a first impression”.
Plastic musical instruments have been around as long as plastic itself. In the 1950s, world-famous jazz musician Charlie Parker played on an early plastic saxophone called the Grafton.
Today, the vast majority of student clarinets from professional manufacturers are actually made of ABS Resin, not wood; and we (Warwick Music Group, manufacturer of pBone plastic trombones and pTrumpet plastic trumpets), have sold over 500,000 plastic instruments for beginners all over the world.
Below are five objections we hear about plastic musical instruments that we have addressed to help you make the right decision for you:
1) Plastic is bad for the environment
Disposable plastics present a huge problem for the planet. According to Greenpeace, “A truckload of plastic enters the ocean every single minute and UK supermarkets produce 800,000 tonnes every year."
Scary stuff, why would you even entertain buying a plastic trumpet and trombone? The simple reason is that plastic instruments are not disposable like bags or straws. They can last many years and in our case are made from fully recyclable ABS plastic. Brass instruments in contrast are actually worse for the environment, use a lot more energy as well as some pretty nasty materials in their manufacturing processes such as lead and nickel.
Plastic can be the more sustainable choice, but that is not a catch-all for every plastic musical instrument maker – far from it. Plastic instrument manufacturers bear an even greater responsibility because, unlike the traditional brass instrument manufacturers who cannot easily change the way they manufacture, it is so much easier for us to be sustainable and greener for the planet.
Make sure you look for the real green credentials of your instrument maker – are they talking about sustainability? The impact they are having and what they are doing to minimise their CO2 emissions? If they’re not then we’d suggest you keep looking.
We recently commissioned some research with Keele University to assess our own impact and are delighted that our hard work around sustainability and the environment has saved the equivalent of over 72,000 trees to date. In fact, since 2020, all of our products have been carbon neutral.
2. Plastic is cheap
That's a strange thing to say - isn't being cheap a benefit?! Well, if you mean value for money then we would agree, that the perception of 'cheap' is sometimes negative; that plastic means low quality compared with heavy dense materials (think gold or platinum) which are expensive and therefore perceived as high quality.
The truth is that plastic will never feel as polished and refined as the most expensive brass metal musical instruments. So if you need a high-end professional instrument then buying plastic is probably not the right option for you (unless there are physical attributes that make holding a brass instrument too difficult, or you want to take it where brass cannot go, like the beach!).
However, if you’re looking for an affordable starter trumpet and trombone then don’t buy 'cheap' buy quality. Anyone who says that you can’t have both high-quality and low-cost is incorrect – we see this all the time in our daily lives (think Ikea, who has done so much for affordable, good-quality home living). You just need to pick a manufacturer who values and demonstrates quality in its outlook.
3) Plastic instruments are toys, not real instruments
When we developed and patented the pBone, the world’s first plastic trombone, it took us three years of getting it wrong before we got it right!
The breakthrough moment came when, as trombonists ourselves, we stopped trying to make a brass trombone in plastic and instead focused on making a plastic trombone. Copying brass instruments in plastic is fundamentally impossible because the acoustics and density of the materials that are completely different.
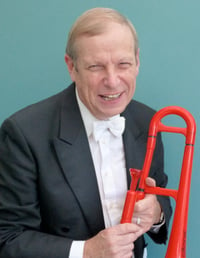
Now some Chinese manufacturers are actually brass and plastic manufacturers at the same time. When you specialise only in making instruments from plastic what you try to do is to provide the customer with all the benefits (i.e. light-weight, robust, affordable, etc) but also deliver an authentic musical experience so that the instrument ‘sounds’ the same to the listener and ‘feels’ the same to the player.
It’s the ethos of the manufacturer that matters most here. Do they care about providing an authentic first experience or are they just copying what they’re already making in brass?
Just because plastic instruments can be colourful does not mean they're toys - we don't expect to see our instruments used at the professional symphony orchestra in a serious performance of Beethoven or Mozart, but our instruments are used by many professional orchestras for school concerts, 4th July or Last Night of the Proms!
That being said, where our instruments are like toys is in their safety features. We take this responsibility very seriously as well as undertake detailed quality checks and safety testing to international standards because we're #seriousaboutmakingmusicfun.
4) Plastic musical instruments don’t sound the same as metal instruments
The answer here depends on the instrument and manufacturer you pick (it also relates to #3 above).
We were recently featured by worldwide publisher Scholastic Education in their Dynamath Magazine, which is distributed monthly to hundreds of thousands of children in schools.
The topic was the maths and science behind our plastic instrument designs, and how we are able to make our trumpets and trombones sound like brass instruments.
Some plastic instruments sound pretty much indistinguishable from metal instruments but only when made well and also differently from metal instruments. If you want to hear how they sound side by side then watch and hear the video below:
Some instruments do not translate as well from metal into plastic. Generally shorter wind instruments are a lot harder to create the sound of real wind instruments so plastic flutes and clarinets haven't become as popular in their markets in the way that pBones and pTrumpets have.
However, one stand-out competitor of ours is the GUO plastic flute which sounds fantastic (it isn’t cheap at almost £1,000!) But it proves the point; plastic instruments can sound the same as metal instruments, you just have to buy the right one.
5) You can’t repair plastic instruments
One of the distinct advantages of metal instruments is that generally metal instruments can be repaired by an expert repairer. Indeed, there are repairers in many established music retail stores and music education establishments around the world.
The problem is if you drop a trumpet or trombone, then it could easily cost you £50/$75 to repair a dent in the trumpet valve block or trombone slide – and these aren’t skills you can do at home, Dad! They require special tools and years of experience.
But it isn’t accurate to say plastic instruments can’t be repaired. They can – in fact, often all that is required is some strong glue. If you buy a quality plastic instrument you are already minimising the chance and cost of going to a professional repairer and when plastic instruments get dropped, unlike brass, they tend to bounce rather than dent.
To be extra safe, make sure you buy from a manufacturer that offers at least a 12-month warranty period and also has good customer support which is easy to access. Read reviews of how the manufacturers you're considering respond to customer problems or issues. Buying from a faceless organisation might save a few pounds or dollars at the start, but won’t be worth it in the long run.
Steven has over twenty years of experience working in the music industry. With degrees in Electrical Engineering and an MA in European Cultural Policy & Administration from the University of Warwick, where he now serves as a Course Tutor on their MA in Creative and Media Enterprises, Steven served as Executive Director of a non-profit international music association based in the United States from 2000 – 2007.
Steven is founder and CEO of Warwick Music Group now known as pBone Music, and started playing the trombone at the age of nine. Based in North Warwickshire, the company manufactures musical instruments that make the joy of music accessible. sustainable and fun including the world's first plastic trombone, pBone, which has sold over 250,000 units worldwide and won major international awards including the prestigious Queen's Award for Enterprise (Innovation) in 2019.
He was elected as a board director for the UK music industry trade body, the Music Industries Association, in 2019 becoming its chair in 2020, and is frequently interviewed or invited to present guest lectures on cultural entrepreneurship, music education, and the future of the music industry. At the request of the owner, Denis Wick, Steven joined the board of Denis Wick Products in 2021 subsequently being appointed their Chief Executive Officer in 2022, a role he performs alongside his role as CEO for pBone Music.
Steven lives in Warwickshire with his wife, Kate, their three young children, two ponies and a faithful labrador, and enjoys coaching his local youth rugby team.
Topics: